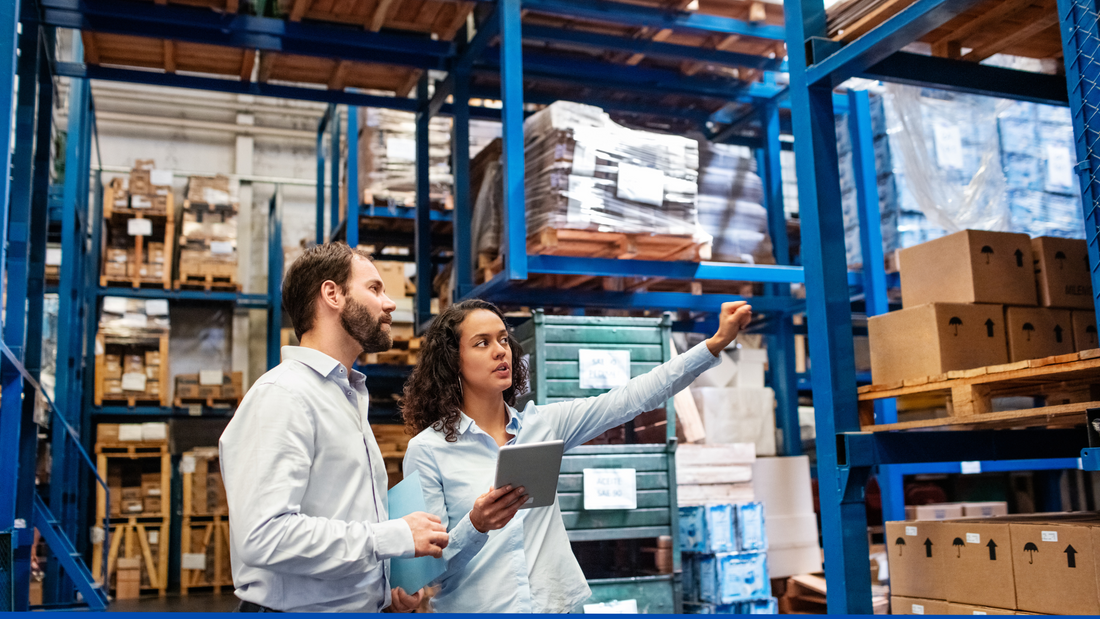
Why Looking at your Inventory Aging Matters for Manufacturers
Share
In manufacturing, inventory is your lifeline. But when stock sits too long, it ties up cash, eats up space, and risks becoming obsolete. That’s where an Inventory Aging Report comes in. It’s like a health check for your inventory, showing you what’s moving and what’s gathering dust. For discrete manufacturers, understanding inventory aging isn’t just helpful—it’s essential for staying lean and competitive.
What Is Inventory Aging?
Inventory aging tracks how long items have been sitting in your warehouse. The report breaks stock into buckets—for example, 0-30 days, 31-60 days, 61-90 days, and over 90 days—based on when they were received. Each bucket tells a story. Fresh stock (0-30 days) is likely in demand, while items over 90 days might be slow movers or obsolete. By analyzing these buckets, you can spot trends, prioritize stock, and make smarter decisions.
Why It’s a Vital Tool
Imagine you’re running a shop floor producing custom parts. You’ve got raw materials, work-in-progress components, and finished goods. If half your inventory hasn’t moved in months, you’re not just wasting space—you’re locking up cash that could be spent on high-demand items or new equipment. An Inventory Aging Report helps you:
- Free Up Cash Flow: Identify slow-moving stock to discount, repurpose, or write off, releasing tied-up funds.
- Optimize Warehouse Space: Clear out old inventory to make room for fast-moving items, streamlining operations.
- Reduce Obsolescence: Catch items before they become unusable, especially for time-sensitive materials like adhesives or electronics.
For example, a manufacturer using Infor VISUAL ERP might notice 20% of their steel rods are over 90 days old. By digging into the report, they could discover a supplier over-delivered or demand dropped for a specific product. Armed with this insight, they can adjust purchasing or negotiate returns, saving thousands.
How to Use It Effectively
Getting the most out of an Inventory Aging Report starts with regular reviews. Here’s how to put it to work:
- Run the Report Monthly: Check aging buckets to catch slow movers early. With iMiner for Infor VISUAL ERP, you can generate detailed Inventory Aging Reports in seconds, complete with clear visuals to highlight trends.
- Drill Down: Don’t just look at totals. Break it down by product category, supplier, or location to pinpoint problem areas.
- Act Fast: If items are creeping into the 61-90 day bucket, consider promotions or bundling to move them before they hit 90+ days.
- Adjust Purchasing: Use aging trends to fine-tune reorder points and avoid overstocking low-demand items.
Real-World Impact
Picture a mid-sized manufacturer of automotive components. Their Inventory Aging Report flags a batch of gaskets sitting for 120 days. By investigating, they realize a client scaled back orders but didn’t update forecasts. The team pivots, offering a discount to clear the stock and reallocating warehouse space for high-turnover parts. Result? They save on storage costs, recover cash, and keep production humming.
Getting Started
If you’re using an ERP system, generating an Inventory Aging Report is straightforward. With tools like iMiner for VISUAL ERP, you can categorize stock by age and costs. The key is to start small, review regularly, and act on what you find.
Inventory aging isn’t just about numbers; it’s about keeping your operation agile. By staying on top of what’s sitting still, you can cut costs, boost efficiency, and focus on what keeps your shop floor moving. Got old stock weighing you down? Run that report and take control.